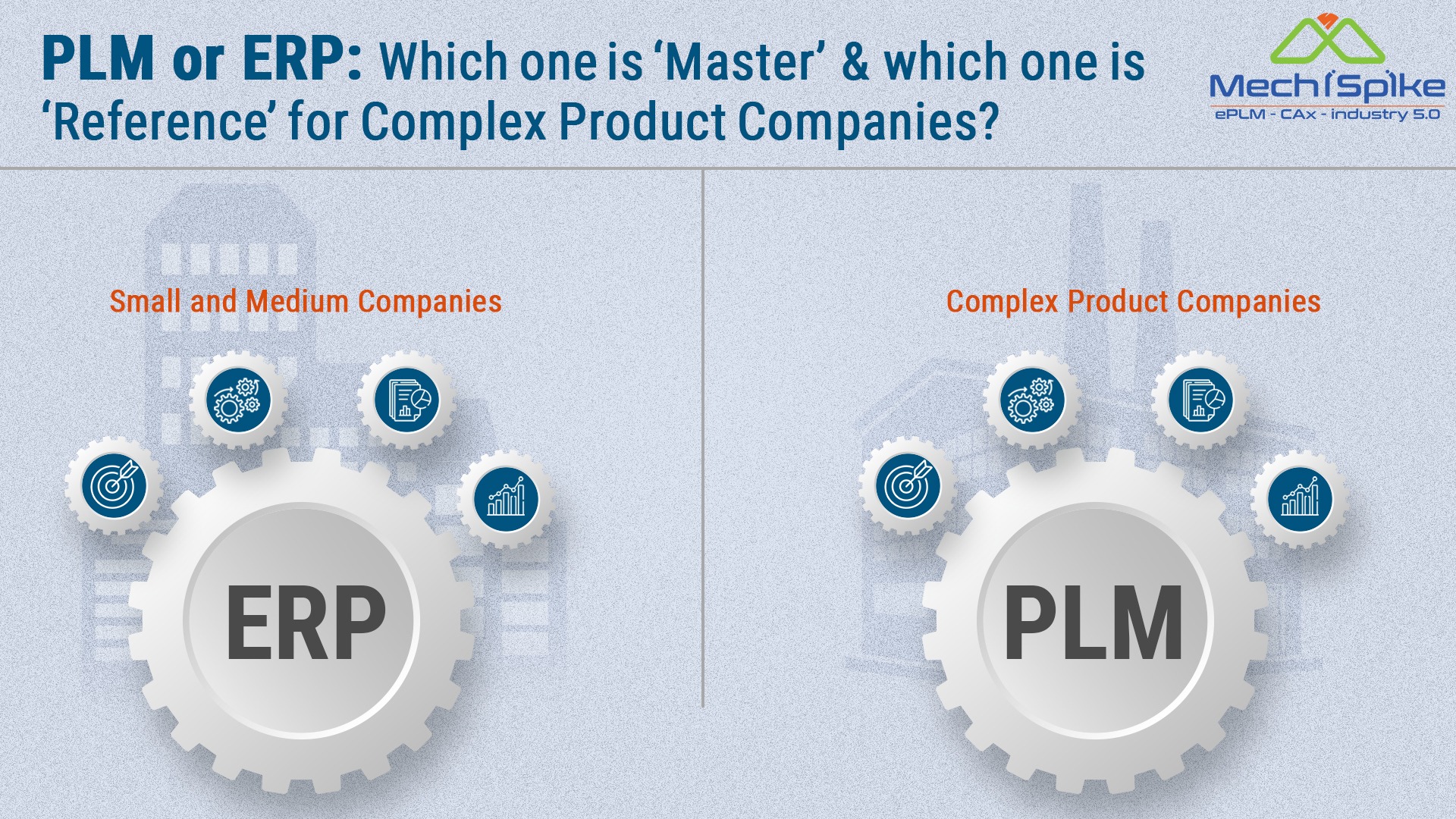
PLM or ERP : Which one is ‘Master’ and which one is ‘Reference’ for Complex Product Companies?
In our weekly journey to better our PLM ROI with this newsletter, last time, we learnt about – How to Write a CV, especially for Niche Areas like PLM.
In this article, let’s look at the Big Picture of the IT Digital Landscape consisting of multiple enterprise applications such as PLM, ERP, CAD, ALM, CRM, MES etc.
In the digital transformation journey of manufacturing organizations, two critical enterprise systems—Product Lifecycle Management (PLM) and Enterprise Resource Planning (ERP)—play significant roles.
Traditionally, ERP has been considered the heart of digital infrastructure, especially for small to mid-sized organizations. However, as businesses scale and their operational complexities increase, PLM takes center stage, orchestrating a broader ecosystem of interconnected applications such as ERP, Computer-Aided Design (CAD), Application Lifecycle Management (ALM), Manufacturing Execution Systems (MES), and Customer Relationship Management (CRM).
This article explores the shift of PLM from REFERENCE to MASTER as organizations grow and become more complex with ERP shifting from MASTER to REFERENCE.
We’ll examine why ERP dominates early-stage enterprises, how complexities necessitate a PLM-first approach, and why large-scale manufacturers must prioritize PLM as the central pillar of their digital infrastructure.
The ERP-Centric Digital Infrastructure: Ideal for Small to Medium Enterprises
Enterprise Resource Planning (ERP) systems are designed to manage business processes such as finance, supply chain, human resources, and order management. For small to medium-sized businesses, ERP is often the central hub that integrates various business functions, ensuring efficiency, cost control, and compliance.
At this stage, ERP systems communicate with other enterprise applications such as Customer Relationship Management (CRM), Human Resource Management Systems (HRMS), and procurement tools. The focus is on streamlining operations, optimizing workflows, and ensuring smooth financial and operational performance.
In a relatively simple business environment, this setup works well. Since product development is relatively straightforward and manufacturing processes are standardized, there’s minimal need for a sophisticated system to manage complex product data, engineering changes, or regulatory compliance beyond what an ERP system can handle.
The Complexity Challenge: Why ERP Alone Falls Short in Large Organizations
As organizations grow, they face increasing complexity in product development, manufacturing, and regulatory compliance. Several factors contribute to this complexity:
- Diverse and Complex Product Portfolios – Larger companies deal with multiple product variations, configurations, and customizations that require advanced engineering collaboration.
- Integration of Multi-Disciplinary Engineering – Modern products combine mechanical, electrical, and software components, making engineering collaboration across CAD, ALM, and simulation tools crucial.
- Stringent Regulatory and Compliance Requirements – Industries such as aerospace, automotive, and medical devices require rigorous traceability and compliance documentation, which traditional ERP systems are not built to handle.
- Global Supply Chain and Distributed Manufacturing – Large enterprises operate across multiple geographies, requiring advanced product data synchronization across suppliers, contract manufacturers, and internal teams.
- Rapid Innovation and Agile Development – Companies must iterate quickly on new designs, requiring seamless change management and collaboration across engineering teams.
In such an environment, relying on ERP as the digital backbone becomes inefficient. ERP systems are excellent at managing transactional data (e.g., purchase orders, invoices, and inventory levels), but they lack the capability to handle dynamic product data, design iterations, and cross-functional collaboration. This is where PLM takes the lead.
PLM as the New Digital Backbone in Complex Product Organizations
Product Lifecycle Management (PLM) is designed to manage the entire lifecycle of a product, from initial concept and design through production, service, and retirement. Unlike ERP, which focuses on financial and operational processes, PLM focuses on managing engineering data, collaboration, and innovation.
As organizations grow in complexity, PLM assumes the central role, with ERP and other systems acting as satellite applications. PLM becomes the MASTER and other systems including ERP becomes the REFERENCE.
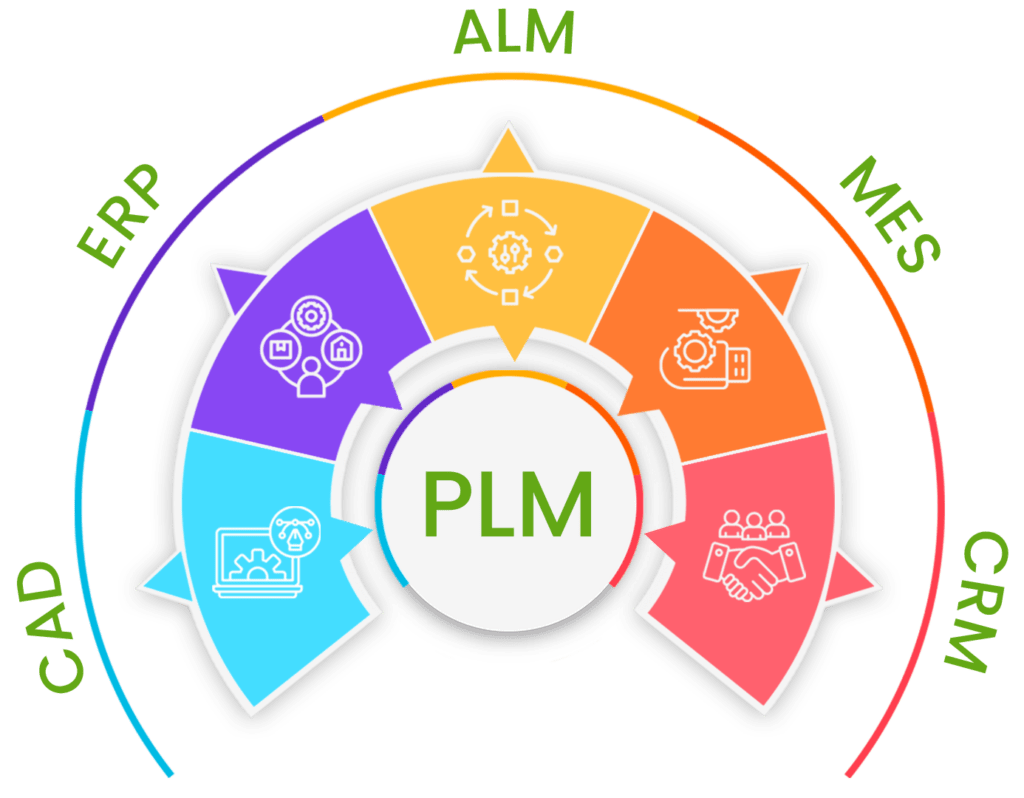
Here’s why:
1. PLM Becomes the Source of Truth for Product Data
- PLM provides a single repository for all product-related information, ensuring consistency across engineering, manufacturing, and supply chain teams.
- It integrates with CAD tools, allowing engineers to manage design data, revisions, and simulations in a structured environment.
2. PLM Integrates with ERP, MES, ALM, CRM, and Other Systems
- Instead of ERP being the central hub, PLM becomes the backbone, connecting various enterprise applications.
- PLM-to-ERP integration ensures that accurate product data flows seamlessly into manufacturing and supply chain systems.
- PLM works with MES (Manufacturing Execution Systems) to ensure real-time production data synchronization and quality control.
- Integration with ALM (Application Lifecycle Management) enables the management of software components within modern smart products.
3. PLM Enables Effective Change Management
- Engineering Change Orders (ECOs) and Change Requests (ECRs) are efficiently handled in PLM, ensuring that design changes are communicated across the enterprise.
- This reduces errors in production and eliminates costly rework and delays.
4. PLM Supports Regulatory Compliance and Traceability
- Industries with stringent compliance requirements benefit from PLM’s ability to maintain full traceability of design changes, approvals, and documentation.
- It ensures that all products meet regulatory standards, reducing risks of non-compliance.
5. PLM Drives Innovation and Collaboration
- By providing a structured environment for engineers and cross-functional teams to collaborate, PLM accelerates product innovation.
- It facilitates concurrent engineering, allowing multiple teams to work on different aspects of a product simultaneously.
Conclusion: The Strategic Importance of PLM in Large-Scale Manufacturing
As manufacturing organizations grow in size and complexity, they need a more sophisticated approach to managing product data, engineering collaboration, and innovation.
While ERP remains crucial for business operations, it is no longer the digital backbone aka MASTER in highly complex enterprises. Instead, PLM takes center stage, serving as the foundation for seamless integration between engineering, manufacturing, and business functions.
For large-scale manufacturers, investing in a robust PLM system is no longer optional—it is a strategic necessity. Organizations that adopt a PLM-centric approach gain a competitive advantage by reducing time-to-market, enhancing collaboration, ensuring compliance, and enabling efficient product innovation.
In the age of digital transformation, the question is not whether companies should implement PLM but how soon they can make PLM the core of their enterprise architecture. The sooner they shift to a PLM-first strategy, the better they can manage complexity, scale efficiently, and drive future growth.
MechiSpike can be of great help to your organization to help you with our PLM, Engineering and IT Digital focus. Click here to know more about this.
For Corporates :
MechiSpike can be of great help to your organization to help you improve your PLM ROI and 30% Savings, be it the hiring cost in staffing or setting up an ODC.
We do this with efficient planning, organizing and controlling Product Master data with seamless data exchange among Engineering, Manufacturing and Enterprise systems.
Why MechiSpike :
Niche Expertise in Engineering & IT
Our Speed of Hiring, Cost Optimized Solutions and Global Presence.
RightSourcing is ‘Better Outsourcing’, given to ‘NICHE EXPERTS’.

For PLM Careers :
Learn More | Earn More | Grow More
Interactive UI : Every Application will get a response with a recruiter contact details and the applicant will get a notification at each phase until the applicant is positioned well with our 15+ global clients in India, USA & Germany.
Candidate Referral Program : Refer a candidate and earn INR 25,000.
Mechispike Solutions Pvt Ltd is a PLM focused company, having all kinds of PLM projects to enable employee career growth and add value to clients. We can position you better with our 15+ global clients in India, USA & Germany.
We believe in “Grow Together” and “Employee First” culture.
Dream more than a Job. Grow your PLM Career to the Fullest with MechiSpike
Click Here to explore our Job Openings.
Subscribe Now :
Our mission : To equip you with the knowledge and tools you need to drive value, streamline operations, and maximize return on investment from your PLM initiatives.
PLM ROI Newsletter will guide you through a comprehensive roadmap to help you unlock the full potential of your PLM investment.
We are committed to be your trusted source of knowledge and support throughout your PLM journey. Our team of experts and thought leaders will bring you actionable insights, best practices, case studies, and the latest trends in PLM.
Subscribe Now to get this weekly series delivered into your Inbox directly, as and when we publish it.
To your PLM success!
Warm regards,
Visit Us: www.mechispike.com